Discover the many factors influencing industrial potato peeler prices and how Vanmark's peelers can boost efficiency and profits in your operations. Learn more.
Having the right potato processing equipment is crucial to improving quality, consistency, and profitability. Potato peelers are an essential component in this lineup, streamlining the preparation process for a wide range of potato-based products.
Choosing a peeler that perfectly aligns with your production needs is instrumental in optimizing operational efficiency and maximizing returns on investment. Vanmark industrial potato peelers are a cut above the rest in terms of features, functionality, and overall value.
Read on as we shed light on the factors influencing the average price of industrial potato peelers and underscore why Vanmark’s potato peelers are a wise and future-proof investment.
Factors That Influence the Price of an Industrial Potato Peeler Machine
Several important factors contribute to the price of a peeler machine. Understanding these aspects will help you make a more informed purchasing decision and ensure the one you choose fully meets your requirements and challenges.
Steam vs. Abrasive Peeler
The initial investment and maintenance costs associated with steam peelers can be substantial. Significant investments are required in utilities and infrastructure to facilitate the generation of pressure and steam necessary for the peeling process. Additionally, the ongoing operation of a steam peeler demands a considerable amount of utility resources.
Abrasive peelers, in comparison, offer a more cost-effective solution with lower initial investment and maintenance expenses. They do not require the same level of infrastructure and utility resources as steam peelers. However, abrasive peelers may result in a less smooth peel surface and may require more aggressive grinding of the potatoes to achieve satisfactory peel removal.
Continuous vs. Batch Peeling
Continuous peeling and batch peeling are two distinct approaches to the peeling process, each offering its own set of advantages and cost considerations.
Continuous peeling keeps produce moving through the machine for a steady output. It's great for large operations because it's efficient and can handle lots of produce with little downtime. However, it requires a greater upfront investment due to the cost of automated equipment.
Batch peeling, on the other hand, processes set amounts of produce at a time. It's good for smaller operations or when there's not a lot of product. Batch peelers are usually smaller and cheaper than continuous ones. They're also flexible in handling different types of produce. But, they need manual work to load and unload, which takes more time and effort.
Choosing between the two depends on factors like the size of the operation, resources available, and specific needs. Large operations might prefer continuous peeling for its efficiency despite its higher initial cost. Smaller operations or those with varying needs might find batch peeling better due to its lower cost and flexibility.
Water Treatment and Maintenance
Maintenance and parts replacement are also factors that influence long-term costs. For example, a rough scrub may wear down rolls faster, meaning more frequent replacements. Buying non-OEM parts can potentially cause increased wear and tear on the peeler.
Also, take into consideration water treatment costs. The Vanmark Water Reclamation System significantly reduces water consumption by recirculating processed water from our abrasive peelers in a closed-loop system.
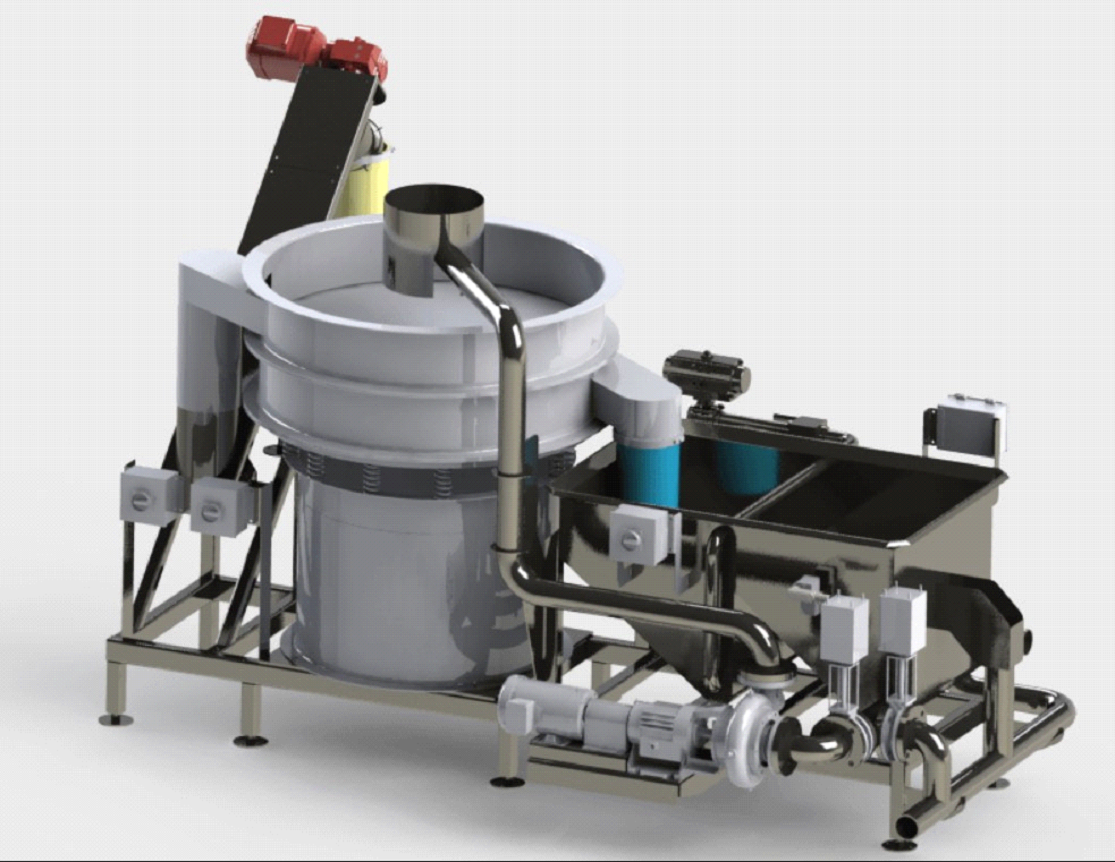
With the capability to support up to three peeler machines, the system allows each peeler to operate on less than 1.5 gallons per minute (5.7 liters per minute) of fresh water. You’ll enjoy a remarkable reduction in water usage by up to 90%.
Size/Capacity
The size and capacity of the peeler influence its price. Larger peelers tend to cost more, but they also allow for greater throughput. For example, Vanmark's 2820 double barrel peeler has an increased capacity and is ideal for large commercial, around-the-clock operations.
Customizations
Customizing your peeler with additional features like Clean-in-Place (CIP), drip pans, discharge gates, etc., can increase the price. However, these essential customizations allow for more efficient and streamlined operations.
Controls
Integrated controls enable increased functionality, such as integration with other machines, automatic stop/start, and more control over the peeling process. While they cost more, they contribute to smoother operations and enhanced productivity.
Rolls
The number and types of rolls in the peeler also affect the price. For specific applications, you might require ones with different textures or materials. Selecting rolls tailored to your products can enhance performance and output quality.
What Sets Vanmark Potato Peelers Apart?
Vanmark’s peelers stand out for several reasons:
Continuous Operation
Vanmark peelers are designed for continuous operation, making them indispensable for large processors and growing businesses. The ability to operate without interruption significantly boosts productivity, as there’s no downtime between batches.
This is especially beneficial during peak seasons or high-demand periods, ensuring that you can meet your production targets efficiently and reliably.
Ease of Operation and Maintenance
Our peelers are simple to operate and maintain. They feature minimal moving parts, simple washdown procedures, and an auto-lube system for larger models. This ease of operation and maintenance reduces the need for extensive training and allows for quicker adaptation by the workforce.
Moreover, the simplified maintenance procedures mean lower chances of operational hiccups and reduced long-term costs, keeping your production line running smoothly and efficiently. This seamless operation ensures a highly efficient and productive production line.
Product Quality and Yield
Vanmark’s peelers are designed only to peel the skin, preserving the quality of the product and reducing waste. This precision peeling ensures that the maximum amount of potato is retained for processing, which is critical for profitability. Consistency in the peeling process guarantees a uniform end product, vital for meeting high-quality standards and customer satisfaction.
Flexibility
Our peelers are versatile and can handle multiple types of produce. They allow for easy adjustments to control the amount of peel removed, which is a boon for maximizing production capabilities. The ability to fine-tune the peeling process ensures optimal output for different products, catering to various market demands.
Durability and Design
The robust construction ensures that our potato peelers withstand the rigors of an industrial setting for a more extended period, reducing the need for replacements and lowering costs. The innovative design ensures that the machine performs optimally. Our peelers are the exact spec for Frito Lay globally.
Higher Volume
Vanmark peelers significantly increase your production capacity by automating the peeling process, allowing you to produce more chips in a shorter time frame. This enhanced productivity opens the doors to accepting additional orders and meeting higher demand, ultimately driving growth and expanding your market presence. With our automated potato peelers, you can confidently scale your operations and realize your business’s full potential.
Price Range
Vanmark’s basic industrial potato peelers range from $30,000 to $165,000. Customizations and options will add to the cost, but considering the standard features, ease of operation, and durability, the investment is worthwhile for long-term efficiency and productivity.
Integration with Existing Equipment
Sometimes the compatibility of a new peeler with the existing equipment in your facility can influence the cost. Vanmark peelers seamlessly integrate with other machines, making the transition smoother and more efficient. This integration may require an initial higher investment, but it will pay off in streamlined operations.
Brand Reputation and After-Sales Support
The brand's reputation and the level of after-sales support they offer are often reflected in the price. Vanmark may have a higher upfront cost, but the peace of mind of knowing that you have a reliable partner is invaluable. Vanmark’s after-sales support is robust, assisting with maintenance, parts, and service, which is crucial for minimizing downtime.
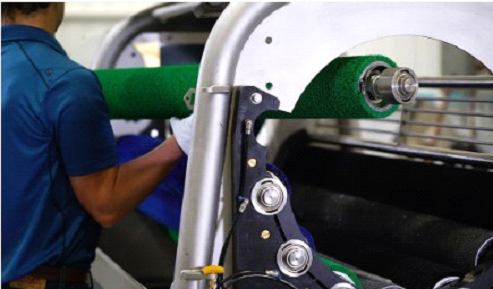
Return on Investment (ROI) and Total Cost of Ownership (TCO)
It's vital to consider the return on investment (ROI). A higher initial investment in a quality peeler like those from Vanmark can lead to lower operational costs and less product waste over time. Investing in a Vanmark peeler means investing in the longevity and efficiency of your production line.
We engineer our peelers for endurance, ensuring seamless performance across extensive production cycles for years to come. With minimal wear parts, the design safeguards your long-term bottom line by reducing maintenance and replacement costs. The result is a lower TCO and quicker ROI.
Future-Proof Your Operations with Vanmark Peelers
When purchasing an industrial potato peeler, it's essential to look beyond the initial cost. Vanmark’s higher price range reflects the added value in terms of standard features, functionality, durability, and ease of operation that you receive.
These factors contribute to a more efficient operation and reduced long-term costs, making Vanmark's peelers a wise investment for your potato processing needs.
Click below to learn more about the value you’ll get from our peeling machines.
See Our Peeling Machines