Vanmark potato and produce peeling machines are well engineered, seasoned and are simple to maintain and operate. They perform a wide range of important high-yield and high-volume tasks—from gently
Vanmark potato and produce peeling machines are well engineered, seasoned and are simple to maintain and operate. They perform a wide range of important high-yield and high-volume tasks—from gently washing to scrubbing to peeling and polishing.
The internal rolls and brushes on Vanmark peelers help achieve this high level of performance. Like all things mechanical, you'll eventually need to replace the peeler rolls and brushes with new ones.
Read on to learn more about peeler rolls and brushes—and the different options and combinations that can impact a peeler machine's performance.
Peeler Rolls and Brushes: OEM vs. Aftermarket
Although there may be alternative suppliers for rolls and brushes at varying price and quality levels, there are a few significant drawbacks to not using and OEM source. As the OEM, Vanmark intimately knows what works best on our machines because we've worked on and tested them for decades—we are the undisputed experts.
We design and optimize our OEM rolls and brushes for a particular machine. There is an excellent chance that a non-OEM brush or roller could negatively impact performance and throughput. Our components are proprietary, so we cannot guarantee that an off-brand roller or brush won't damage the equipment.
Aftermarket products may have a much shorter lifespan due to inferior-quality materials and poor craftsmanship. This directly translates into increased downtime as you may need to stop the line to change out the aftermarket rollers and brushes more frequently than with OEM ones.
Types of Peeler Rolls and Brushes
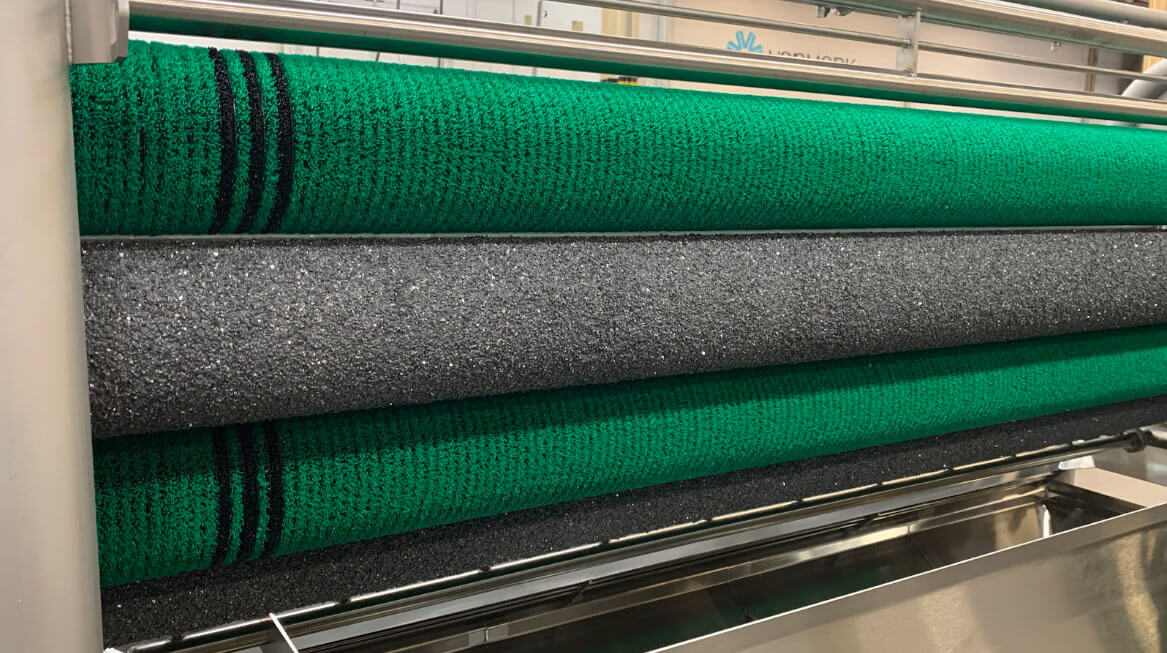
Vanmark rolls and brushes are available in a variety of types, stiffness or coarseness, and in full or half-lengths that allow you to customize the roll configuration to achieve the results your application requires. Many applications require a mix of brushes and/or abrasive rolls for optimal performance; Vanmark's years of experience with potato and produce processing helps us to consult you on the best configuration for your needs.
The high quality of our peelers extends to our selection of various OEM rolls that provide consistent performance. Our peeler brush/roll types and associated applications include:
Brushes—are most commonly used in our peelers to wash, peel, and scrub the product while removing dirt, debris, and the desired amount of peel while minimizing yield loss. Used on a variety of products and applications -- from gently washing cucumbers to peeling potatoes on a potato chip line. Brush life will vary based on a variety of factors such as product type, application, throughput and whether you're running storage or fresh crop
Coated Abrasive—frequently used for peeling, rough scrubbing, and polishing a product – leaving a smooth surface. Available in a range of abrasiveness from very fine grits used to polish baby carrots to more aggressive grits used to peel potatoes.
Lift Roll—a smaller diameter roll that separates solids and tumbles the product while keeping the chamber cleaner after steam peeling.
Rubber Pintle—used to collect loose residue after steam peeling. It helps keep the peeler clean.
Sinewave Segment—timed mechanically to synchronize segment movement to abrasively peel odd-shaped products.
General Care and Maintenance
There are a few general maintenance tasks that you can do to increase the effectiveness of your peeler rolls/brushes and supporting parts (bearings, shaft, couplers, etc.) while limiting downtime for changeouts.
- Always keep spare inventory for change-outs on hand. This will help you avoid shipping, handling, and potential availability delays.
- Monitor the performance of the peeling machines to determine the optimal time for roll and brush changeouts. Key indicators include bent bristles and needing to keep product in the bed longer to achieve the same peel level.
- Cleaning and regular maintenance are critical. Our Clean In Place (CIP) system automatically cleans the rolls and peeler bed during production and sanitation in less than 10 minutes. This helps to significantly reduce manual cleaning and the resulting downtime.
Here's an informative video on how to change the rolls on a Vanmark Peeler/Washer/Scrubber machine: