Industrial produce and potato processing equipment offer your food production line several distinct advantages, such as increased yields, decreased waste, and reduced labor requirements.There are
Industrial produce and potato processing equipment offer your food production line several distinct advantages, such as increased yields, decreased waste, and reduced labor requirements.
There are several important factors to consider when evaluating the total cost of equipment investment. Instead of just focusing on the initial cost, consider operation costs, aftermarket parts and maintenance, the impact on your production rates and downtime, as well as the life of your machine. All of these factors can help you make a more informed purchasing decision.
Why Calculate TCO?
Whether you’re looking to automate a portion or the entirety of your produce processing line, calculating the TCO of the machinery will enable you to determine if the capital investment will pay off in the future. This exercise will also provide valuable insights into the areas of your business that necessitate improvements to ensure sustained growth.
Calculate Initial Costs
In addition to looking at the initial price of the machinery, consider these associated costs:
- Freight to your facility
- Installation and setup
Calculate Ongoing Costs
After you’ve determined the initial outlay, it’s now time to look at ongoing costs, such as:
Service—Scheduled or emergency maintenance.
Repair and downtime—How would repair downtime affect your costs?
Processes—Do your methods require additional steps? Production rates and processing time (current and future) can affect the ROI.
Parts — What are the costs of replacement parts for machinery when routine use causes things to wear out?
Utilities — Determine potential upgrades for electric, water and air, and estimate ongoing utility costs
Product Yield —Produce has additional associated processing costs such as waste, scraps, giveaway, and rework time. More expensive produce coupled with poor equipment performance means costs and rework time will start to add up.
Labor—There are many different cost considerations for labor. In addition to wages, include benefits, insurance, and 401k matches. The cost per worker start to add up very quickly—to the point where automating certain processes helps achieve a much quicker ROI.
Additional Considerations
When evaluating the TCO of commercial produce processing equipment, there are several other considerations to keep in mind:
Sanitation and Maintenance—How quick and easy is it to clean, maintain, and sanitize? Does the equipment have a sanitary design (washdown rated, open frame, toolless, and fast changeouts)?
Ease of Integration—How easy is it to add the machine to your existing process/line? Will it cantilever over your existing belt, or does it have a built-in one available in left/right configurations? How many workers and how much space does it require?
Production rates—What are your current and potential production rates?
Operation—How easy is it to train and use? Is there a huge learning curve?
Functionality—Do you need single or multiple applications? Are there built-in safeguards to prevent bruising and product damage?
Durability—Can the machine run for an extended period over days/weeks with zero issues?
Evaluate the Manufacturer
Purchasing industrial produce and potato processing equipment is a fairly significant investment on more than a financial level. You’re entrusting the equipment to improve processes on your production line—and maintain your stellar reputation through high-quality processed produce.
Therefore, it’s critical to take a good hard look at the manufacturer to determine the level of service and support you’ll get. Try to answer the following questions:
- Can you send your product to the manufacturer for them to demo their machines with your exact processes before you make a purchase?
- What kind of support does the manufacturer provide over the machine's lifetime?
- How well do they know and understand their equipment in relation to your needs?
- How big is their parts department, and how quickly can they get a spare part to your front door in a maintenance emergency?
- Is there a warranty, and what are the terms?
Is it Time to Purchase Industrial Produce & Potato Processing Equipment?
Once you understand the factors which determine the Total Cost of Ownership, you’ll be able to answer the following questions:
- Should we purchase now or at a later date?
- What is the profitability of this machine?
- When will we realize payback—within two years or less?
- Will the new machine provide a net gain or loss?
Vanmark Industrial Potato & Produce Processing Equipment
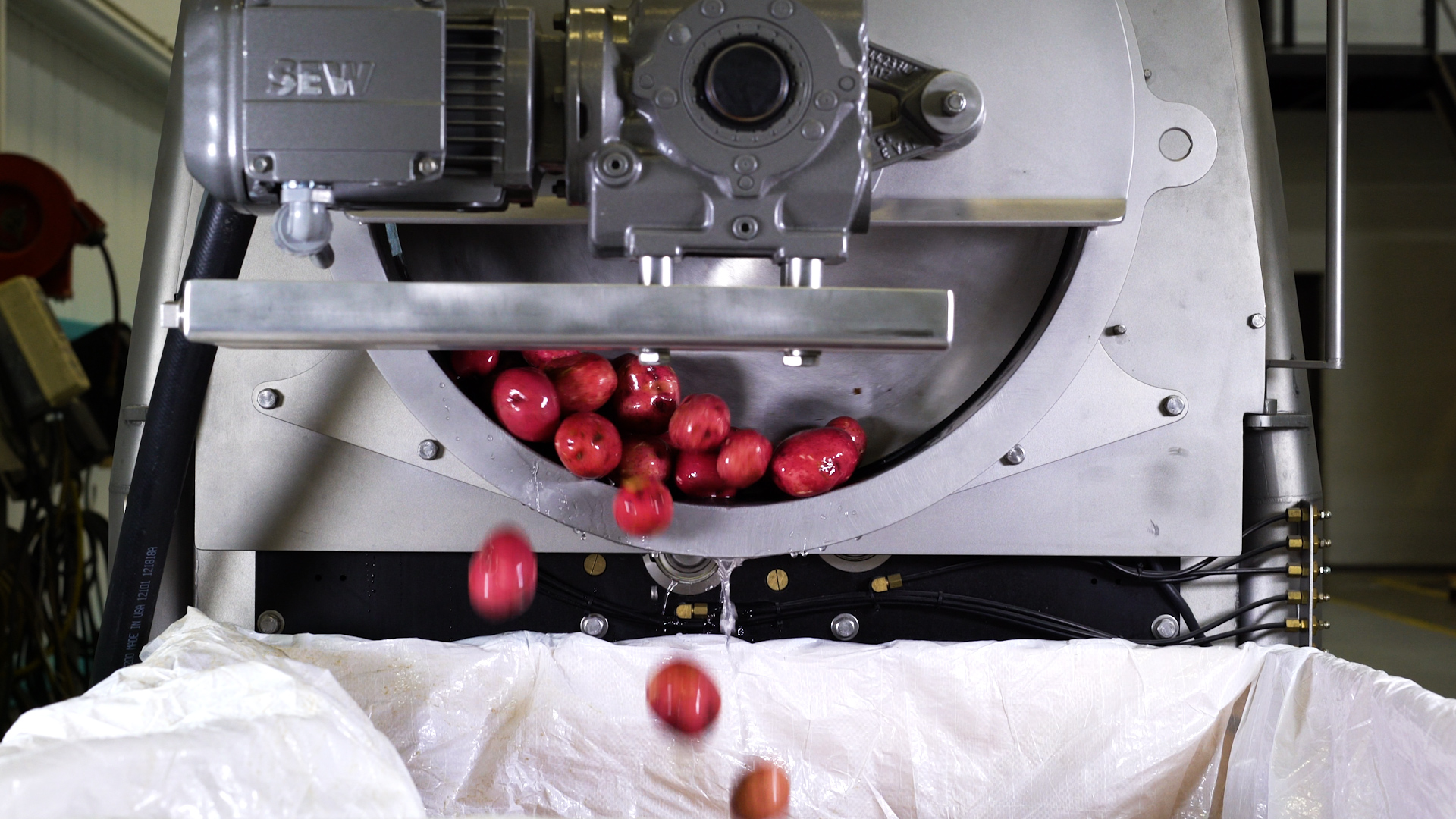
At Vanmark, we designed our produce processing machinery to operate durably over long production runs for years at a time. We achieve this in part by utilizing limited-wear parts on our machines.
There are several durability advantages that Vanmark equipment has over the competition:
Durable Parts/Less Downtime — We only use high-quality parts (bearings, rolls, etc.) manufactured to last as long as possible and only require changing one to two times per year. There may be a higher initial cost, but less maintenance and replacement parts rapidly make up for it. You’ll only need to replace the hydro tubes and consumable blades every 1+ years—this translates into minimal (next to none) maintenance downtime. The simple changeouts will allow you to get back to production quickly.
Ease of Use/Low Maintenance — We design our machines for low maintenance (less moving parts) and simplicity. This translates into low downtime with quick, simple changeouts to quickly get your line back to production.
A More Cost-Effective and Efficient Way to Process Potatoes & Produce
At Vanmark, we designed our industrial produce and potato processing equipment to achieve long production runs for years at a time. Our fleet of machines is vast, many of which can help partially or fully automate your production line.
Click below to learn how a food processor eliminated three manual processes and more than doubled capacity by automating a section of their processing line.
How One Processor Automated Their Line