Vanmark manufactured and installed a new Bulk Storage Bin System for Backer’s Potato Chips—improving production and efficiency. Read more.
Backer’s Potato Chip Company is a family business started in 1931 by Grandma and Grandpa Backer on the bank of Hillers Creek in Callaway County, Missouri. Today Backer’s processes 7,000 pounds of potato chips per hour in its facility. However, the company has faced multiple challenges in keeping up with product demand.
Their existing bulk bin system was decades old and deteriorating quickly, resulting in performance and production issues. They turned to Vanmark to replace it and optimize their receiving area.
Backer’s has a decades-long history with Vanmark and many legacy machines in its facility. The potato chip producer selected Vanmark to fulfill this need because of the durable operation of its existing equipment and the support the company has received over the years.
The Challenge
Their existing bulk bin storage system required unplanned maintenance regularly, impacting production and increasing aftermarket costs. It only featured a single discharge to flume systems which caused additional production bottlenecks. Finally, were experiencing rapid wear of parts at “drop points.”
The Backer’s team visited Vanmark’s Creston, Iowa, facility to see the Bulk Storage Bin System equipment. After witnessing the system in action, they placed an order for it and supporting conveyors.
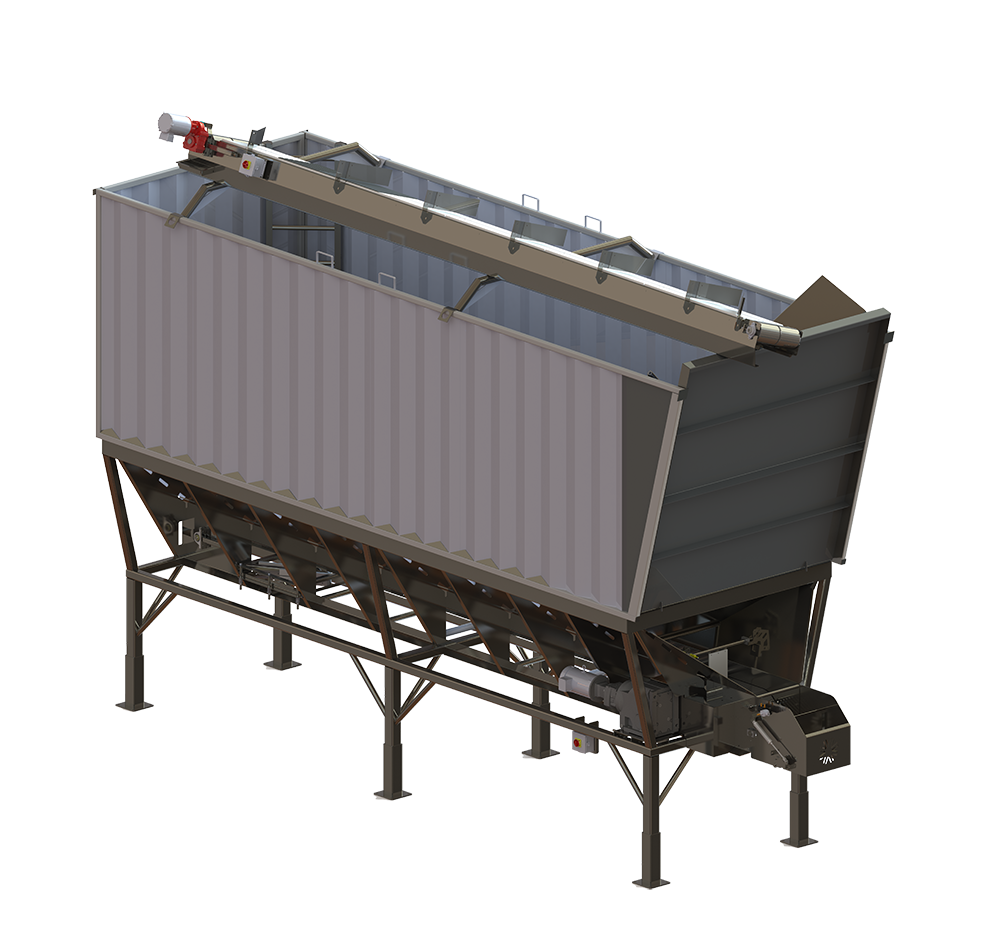
The Solution
Vanmark’s Bulk Storage Bin System receives potatoes and temporarily holds them until they’re ready for processing. The design’s modularity allows the bins to share interior walls. It’s built for flexibility, durability, and gentle product handling.
The system offers multiple discharge points, allowing Backer’s to discharge product to either flume system instead of choosing one. Its surrounding catwalk improves accessibility.
A six-bin system was designed to support Backer’s production performance.
Vanmark’s sister company, PFI, installed the system. The ease and cost savings of turnkey equipment and service attracted Backer’s.
Now
Pleased with their new system, Backer’s no longer has to worry about repairing outdated equipment, and the speed of their unloading process has increased dramatically.
The time saved has allowed Backer’s to focus more time and attention on growing its business.
Download the full case study.