Discover the hidden costs in your potato chip receiving and preparation processes. Strategic equipment upgrades can boost efficiency and profitability.
Potato chip production is a complex process with many moving parts. Manufacturers need efficient, reliable, and purpose-built equipment to maximize profitability and meet growing consumer demand. Vanmark offers easy-to-use, high-quality machines which help improve the receiving and preparation processes in a potato chip processing line.
Using outdated or substandard potato chip processing equipment can result in substantial financial losses. However, that’s nothing compared to the potential for lost contracts and harm to your brand due to poor-quality chips making their way onto store shelves.
Discover how to optimize and ultimately save money throughout the following equipment areas and production processes:
● Receiving
● Short-term storage
● Washing and peeling
● Supporting equipment
And how upgrading to Vanmark equipment can significantly improve your bottom line.
Receiving - The Start of Your Potential Problems
The receiving station is the critical first step in potato chip processing. Efficiently moving products from delivery trucks into the facility and onto the production line is essential for smooth operations. Inadequately designed receiving equipment can lead to many issues that threaten operational efficiency and product quality.
There are several ways your receiving equipment could negatively impact operations and profitability:
Product Handling—Efficient potato intake starts with a properly designed short-term storage station. Bulk bins should have ample ventilation and delicate handling features to avoid overheating, bruising, or damaging the potatoes. Oversize flume systems with sturdy, automated controls can smoothly handle high potato volumes without bottlenecking.
Dumper Engineering—Potato dumpers must be engineered to avoid the free-fall drops that cause bruising. Insufficient dumper capacity requires inefficient hand-dumping methods that cannot match automated equipment's consistent flow.
Destoning—Poor-quality destoning equipment often falls short in removing all rocks and non-floating debris from the product line. It’s very challenging to keep these subpar machines running properly and prevent them from clogging up.
Unremoved debris, dirt, and stones result in product damage, production halts, broken equipment, and the potential for contamination. These issues lead to increased hands-on labor, thus reducing operational efficiency while driving up labor costs.
Investing in advanced destoning technology, such as washers, hydrolifts, and flume systems significantly improves product quality and optimizes processing. Potato processors looking to boost efficiency and output should upgrade destoners and related equipment as a top priority.
Equipment Durability—Receiving equipment must be highly durable to withstand high-volume, non-stop operations. Outdated or low-quality components lead to breakdowns and line shutdowns. With potato harvesting concentrated in peak seasons, downtime can mean losing revenue from high-demand periods.
Lack of Automation—Manual processes not only slow down production but also increase the risk of inconsistency and unreliability in your operations. Inefficient staffing and a tight labor market can drive up costs, including hiring, training, and workers' compensation benefits.
Continuous Production—Automating the receiving process allows potatoes to be safely, consistently, and smoothly transferred to the start of the processing line. Upgrading to automated equipment helps keep the peeling and frying stages supplied for continuous production.
Maintenance—High-maintenance equipment can be a productivity bottleneck, forcing you to pause operations frequently and focus on time-consuming maintenance routines. Equipment that is challenging to maintain may also require specialized skills or additional personnel, driving up labor costs.
Peeling - Increase Yield and Quality
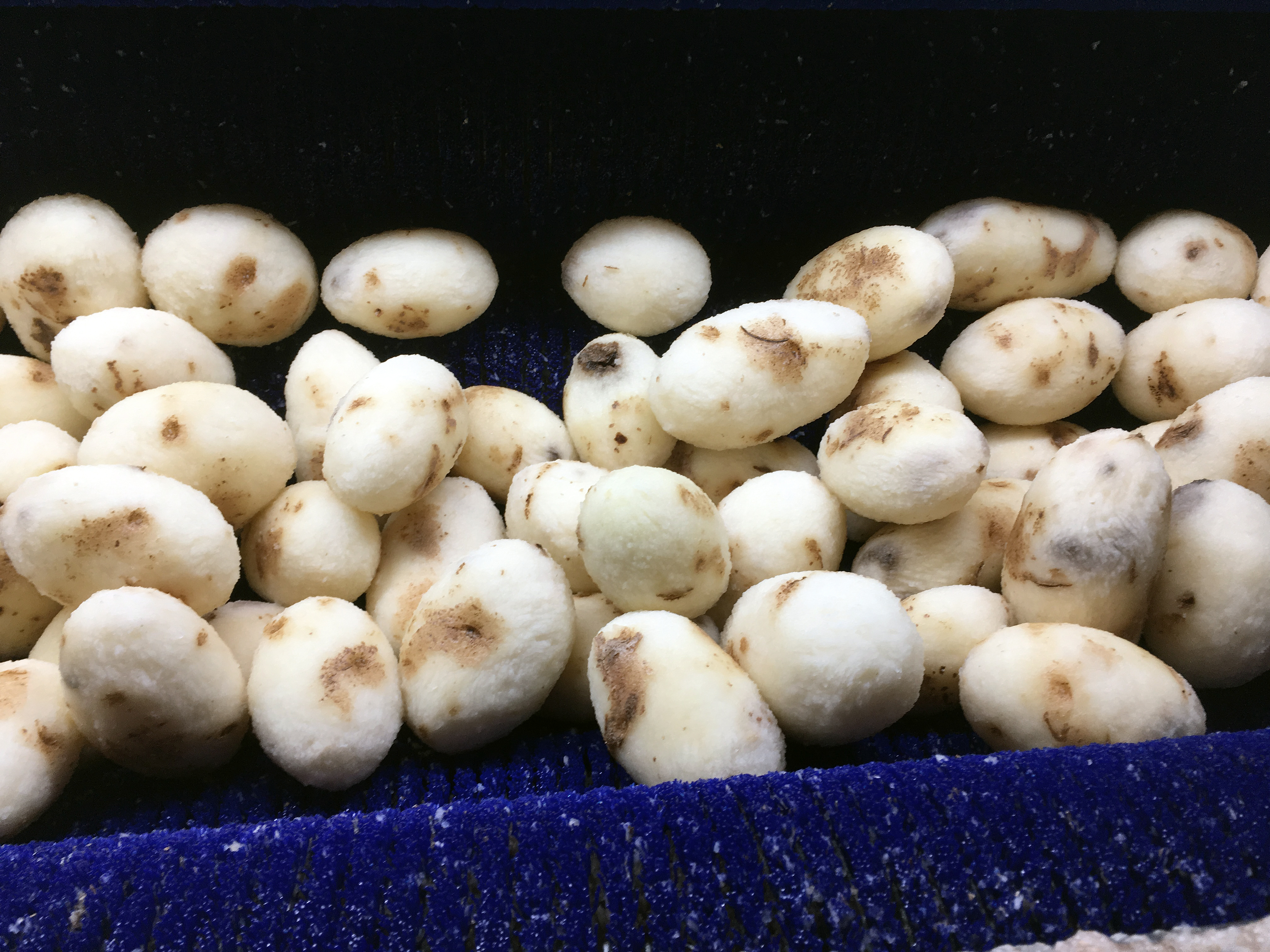
Efficient potato peeling and high-quality machines are essential for maximizing chip yield while producing a high-quality end product. Poor quality equipment reduces yields and compromises chip quality.
You'll wind up needing more raw materials to meet the same production goals. This is a significant and expensive setback considering that potato prices fluctuate and often rise. Poor quality chips impact retail contracts and consumer purchasing in a highly competitive market.
Common equipment shortcomings that lead to these problems include:
Frequent Maintenance and Parts Replacement—Poorly designed peelers that are difficult to access and maintain require lengthy downtime for cleaning, sanitizing, and repairs. Frequent breakdowns require constant parts replacement, but waiting for out-of-stock parts leads to even longer downtimes.
Capacity Constraints—Outdated peelers with insufficient capacity act as a bottleneck, limiting your ability to take on large orders and maximize revenue potential. Running peelers at maximum capacity leaves no room for production growth or surge requests.
Yield and Quality Reduction—Ineffective peeling leads to more waste, requiring you to purchase higher volumes of raw potatoes. Bruising and damage from subpar peelers also harm end product quality.
Water Consumption—Peelers utilize a substantial amount of water during processing, resulting in high freshwater usage and wastewater treatment costs. Incorporating a dedicated water reclamation system allows peelers to recycle process water instead of discarding it after a single use.
The most impactful water conservation solutions use an auger to separate starch and solids from the used process water. Filtering out these particles reduces the amount of water sent for energy-intensive treatment. The filtered water then gets sent back into the system instead of discarded.
Reliance on Manual or Semi-Manual Processes—Continuous potato chip production relies on steady, uninterrupted material input that manual processes cannot provide. Surging then starving the line disrupts the flow and reduces efficiency.
Manual peeling operations are incredibly labor-intensive. They require hiring, training, managing, and paying teams of workers. Labor costs, workers' compensation, and compliance add up quickly. Manual methods also compromise speed, throughput, and product consistency.
Semi-automated lines improve throughput but still require direct staff oversight. Adding supporting equipment like feeders and platforms can streamline partially automated processes. However, skilled workers are still needed to manage equipment and monitor product flow.
Batch Process vs Continual Operation - Upgrading to a continuous operation instead of a batch process for your potato processing line can further increase production, and potentially your profits. While continuous equipment allows near-infinite scaling and throughput, it requires additional investment, and may not be appropriate for all situations. It’s a good idea to review factors which may justify upgrading from a batch process to continuous operation before deciding which is best for your situation.
Supporting Equipment - Hidden Costs Lurking
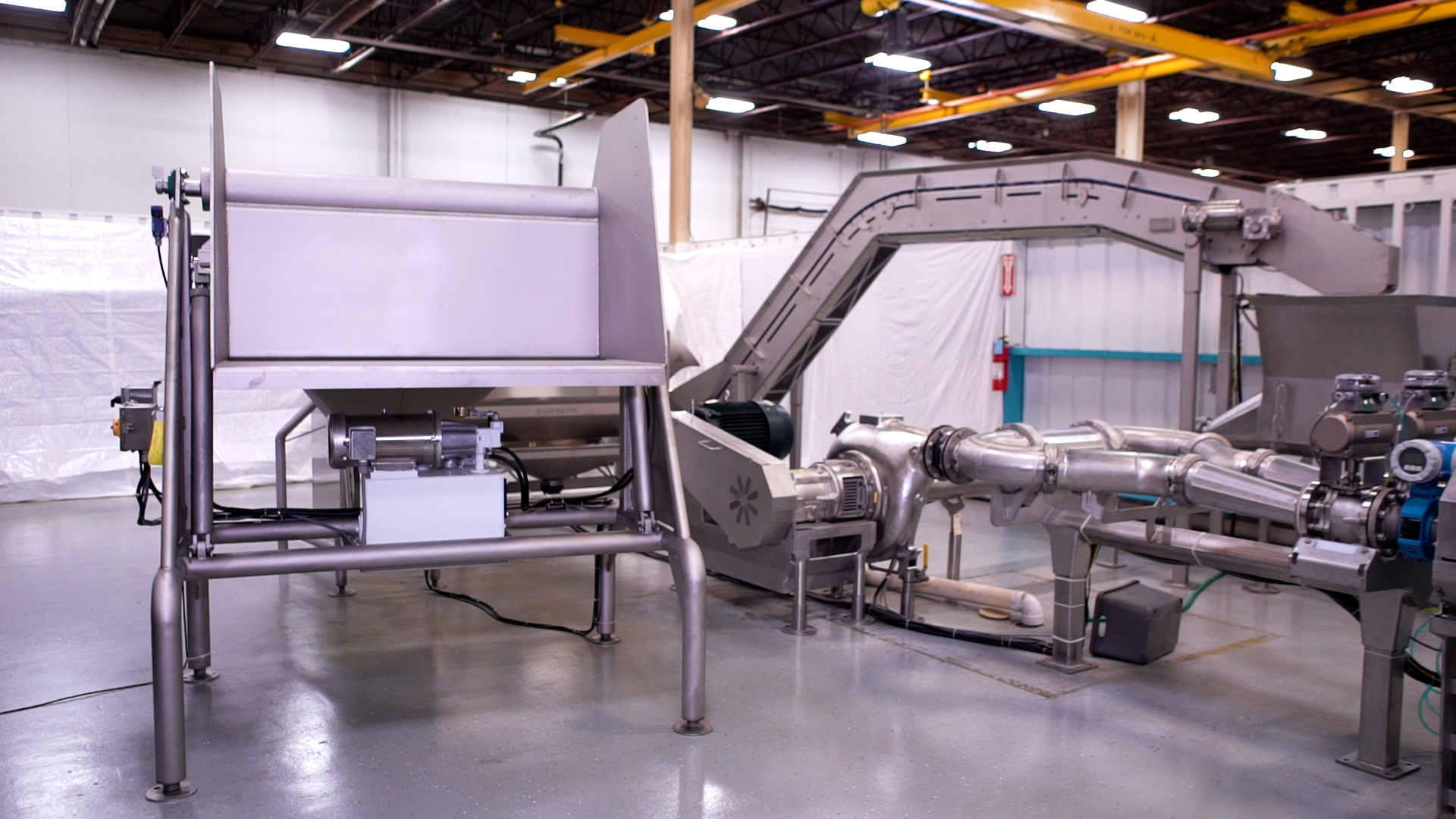
Platforms, catwalks, transfer conveyors, and inspection conveyors can conceal costly inefficiencies. The following and often-overlooked supporting equipment aspects can gradually erode profits:
Outdated Infrastructure—Supporting equipment is critical for an optimized process flow. Outdated or missing supporting infrastructure creates major bottlenecks that limit production speed and capacity.
Maintenance Challenges—Without proper platforms and catwalks, maintenance staff must climb unsafe ladders to access equipment. This makes servicing machines labor-intensive, requiring dedicated operators per piece of equipment.
Manual Material Handling—Insufficient conveyors mean the product must be moved manually between each process stage, consuming time and labor.
Quality Control Issues—Lack of inspection systems forces staff to manually monitor product quality, which is inconsistent and highly prone to human error.
Equipment Reliability—With baked potato chip production lines running nonstop, regular maintenance and repairs on dilapidated supporting equipment eat into production uptime.
Upgrading supporting equipment can reduce accidents, minimize manual labor, improve quality oversight, and maximize production capacity. This translates directly into higher efficiency and profitability.
The Solution: Upgrading to Vanmark Equipment
Partnering with an experienced equipment manufacturer like Vanmark allows potato chip producers to modernize their processes and save money. We engineer our industrial potato processing machinery and systems to withstand the rigors of 24/7 operation with minimal maintenance requirements.
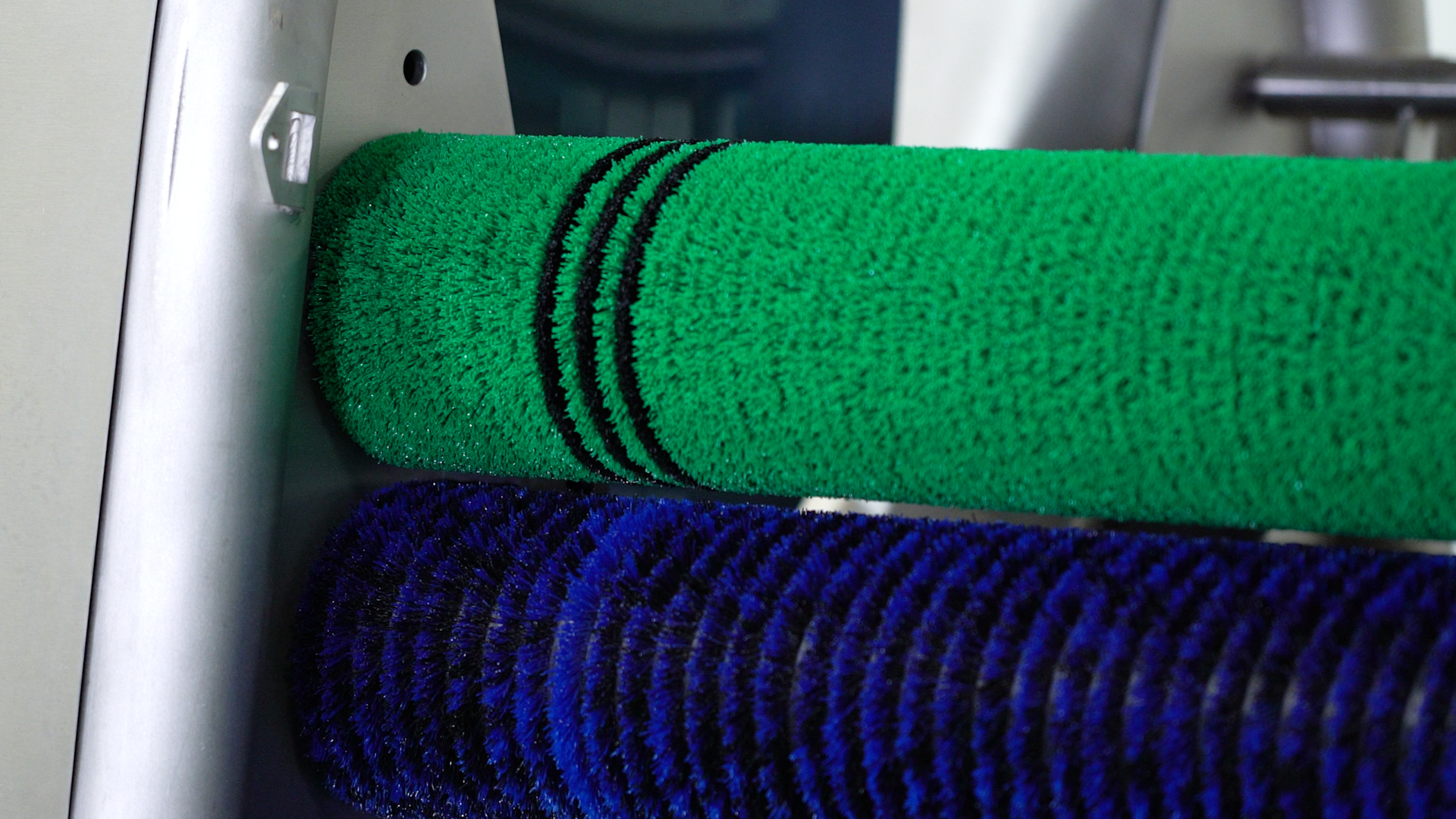
Benefits of our equipment include:
Maintenance and Sanitation—Vanmark potato peelers offer easy maintenance access and tool-free part changeouts that reduce service disruptions. For example, our automated Clean-in-Place (CIP) systems clean the peeler bed and rolls during operation in under 10 minutes. Hands-free sanitation replaces tedious and time-consuming manual scrubbing.
Durable Design—We expertly design and engineer our equipment using high-quality components. This superior construction quality extends the lifespan of our machinery, ensuring optimal performance even in high-demand production environments. As a result, your operation gains a robust, resilient asset, significantly reducing interruptions and contributing to sustained profitability.
Reduced Labor Requirements—Automated equipment and full production line integration lessen the need for manual oversight by skilled workers. Automating your line cuts labor costs and training requirements and is an invaluable benefit in a tight labor market.
Water Conservation—Our Water Reclamation System recycles process water from peelers, using augers to filter out solids. The closed-loop system reduces freshwater usage by up to 90% and significantly decreases wastewater treatment. You’ll enjoy substantial savings in water, sewer, and treatment costs savings.
The Vanmark Waste Separating Auger filters solid peel waste from the process water before recycling. Peels are removed through a self-cleaning screen to be collected and sold. Its compact size allows installation next to the peeler without disrupting line flow. This further reduces wastewater volumes and provides additional cost savings.
Seamless Integration—We design our equipment to integrate seamlessly into new and existing potato chip production lines. Our highly experienced and knowledgeable engineers will work closely with you to ensure a smooth and efficient equipment transition.
Consistent Quality—Precision equipment engineering delivers highly consistent processing for maximum usable yields and end-product quality. You can rely on Vanmark machines to deliver optimized results day after day.
Unmatched Experience—With decades of expertise working with leading chip producers, our knowledgeable team understands the industry and can expertly tailor solutions to your operational needs.
Profit-Boosting Potato Processing Line Equipment
Vanmark has 60 years of experience providing high-quality, easy to use equipment. Upgrading to Vanmark's innovative lineup of equipment offers a wide range of tangible benefits that drive enhanced operational efficiency. You’ll be able to increase production capacity, reduce downtime, improve product quality, and cut labor costs.
Contact us today to learn how our receiving and processing equipment can enhance the profitability of your potato chip production line. Our team of experts will help take your manufacturing operation to the next level and beyond.