Using a manual or mechanical system to cut cucumbers can lead to a wide range of challenges, such as: Maxed-out production Inconsistent quality Labor issues Inefficiencies Sanitation Higher
Using a manual or mechanical system to cut cucumbers can lead to a wide range of challenges, such as:
- Maxed-out production
- Inconsistent quality
- Labor issues
- Inefficiencies
- Sanitation
- Higher maintenance costs
These are just a few reasons why many industrial pickle processors are now adding a hydrocutter to their processing line.
Read on to learn more about increasing quality and capacity while decreasing labor costs with a Vanmark hydrocutting system for your commercial pickle processing line.
Mechanical Cutting
Mechanical cutters are one of the more common methods of processing pickles.
Pickle processing operations use a variety of mechanical cutters that may include some level of automation and/or manual labor. These industrial pickle processing machines often have quality control issues, high maintenance costs, and increased downtime due to frequent breakdowns.
The Vanmark Hydrocutting Method
Hydrocutters use water to transport and accelerate food products through a series of fixed blades. The hydrocutting system works best for high volumes of long products, such as cucumbers for pickle processing. The result is a superior cut quality and yield over mechanical cutting machines.
Hydrocutting Benefits
A single hydrocutter could replace anywhere from two to three mechanical cutters; a twin hydrocutter may replace up to four mechanical cutters. The bottom line is hydrocutting allows for far greater throughput. Since hydrocutting systems have almost no moving parts, maintenance costs are significantly reduced.
At Vanmark, we offer two hydrocutting systems, the Lamina—the standard for industrial pickle processors—and a more compact skid designed for seasonal, specialty, or growing operations.
The Lamina system is custom configured and designed using CFD analysis and comes with a product infeed, pump, motor, acceleration tube, hydrocutter, decelerator, and return water system. There are many benefits that Vanmark hydrocutters will offer your pickle processing line.
Increased Processing Volume
Most cucumbers for pickle processing range in diameter from 1” to 2”. At the smaller end, a single-cutter Vanmark system can hit around 7,000 lbs per hour and closer to 12,000 lbs per hour on the larger end. A twin hydrocutter could double those rates.
Improved Sanitation
The hydrocutting system is designed with stainless steel components and minimal moving parts to ensure thorough sanitation and cleaning. This method is very sanitary because the majority of the hydrocutting system is a closed system with air only present at the infeed and water return tanks.
The ease of the sanitation process for Vanmark hydrocutters provides flexibility for pickle processors to meet their specific sanitation requirements.
Sustainability
Our fully automated pickle processing line uses a closed-loop water system. Once the pickles are cut, the water goes through a return line to the start of the process.
Increase Uptime
Unlike the mechanical cutting method, hydrocutters have almost no moving parts, significantly reducing downtime and costs associated with maintenance and wear-and-tear. Mechanical cutters are very time-consuming and expensive to maintain, especially those in pickle plants. Changeouts and changeovers involving tubes or blades are much faster on the Lamina Hydrocutter due to its tool-less removal feature.
Quality
Over the decades, Vanmark has built a solid reputation for our machinery's high quality and durability. We use superior parts and design our systems to stand up to the rigors of repeated, heavy usage.
Case Study: Industrial Pickle Processing in Action
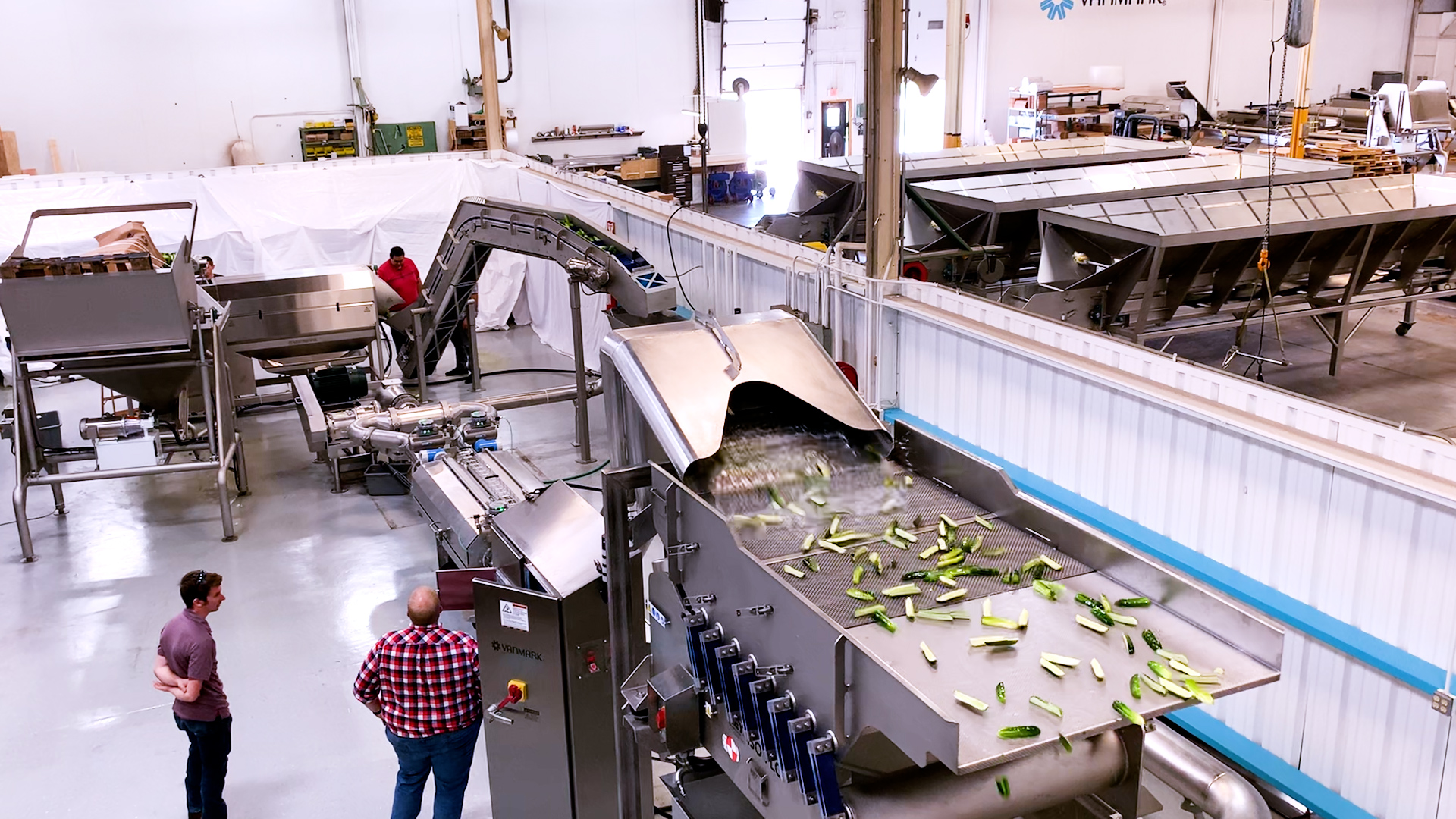
A pickle processor and co-packer was using a mix of inefficient machinery and manual labor processes to load, wash, and cut cucumbers. This resulted in several issues such as poor quality, waste, and maxed-out production. They turned to Vanmark for help automating the entire process into one, single line for multiple processes.
We custom-tailored our fully automated pickle processing line to fit their exact footprint—including through a wall. The solution we provided allowed the pickle processor to eliminate three manual processes, doubled capacity to 12,000 lbs/hr., and increased the overall quality of the final product.
A Fully Automated Pickle Processing Solution
Until recently, there wasn’t an all-in-one processing solution for industrial cucumber processing equipment. That all changed when we introduced our fully automated pickle processing line, that includes receiving, washing, and hydrocutting equipment.
In addition to being a turn-key, fully automated solution, it includes controls to operate the entire system to thoroughly wash the cucumbers and then precisely cut them into spears before gently transferring them for pickling and jarring.
A More Efficient Way to Process Pickles
Vanmark processing equipment will increase efficiency, reduce labor requirements, and improve your bottom line. We carry a wide range of pickle processing equipment that can handle everything from raw receiving through cutting the product. Click below to learn more.
Industrial Pickle & Cucumber Processing Equipment