Discover how our commercial potato peelers can help you scale up production, save money, and reduce labor requirements. Click to learn more.
If you are a small or regional potato chip manufacturer ready to expand your production, Vanmark continuous potato peeler machines will allow you to scale up production without hiring additional workers.
Running Vanmark abrasive peelers that peel, scrub and wash on your line offers increased productivity, efficiency, quality, and sanitation.
Read on to learn more about how Vanmark peelers can help grow your potato chip production operation.
Increase Capacity
The fastest way to increase your facility’s production is to increase the capacity of your equipment, and moving from batch processing to continuous processing will further increase your production.
Continuous operation lets you achieve high throughput with no stopping or starting. You’ll be able to make real-time adjustments while having a higher fryer capacity and larger output on the line. The improved output allows for increased yields.
Batch processors can’t run a continuous feed like Vanmark peelers can. Our continuous, abrasive peeler machines are easier to maintain and usually cost far less in the long run, due mainly to the high maintenance costs of batch processors.
Vanmark continuous automated potato peelers allow you to increase production through a wide range of flow rates. For example, the 1820 series offers a standard flow rate of up to 4,000 pounds per hour. For higher capacity, the Peeler/Scrubber/Washer – 2820/2822 has a standard flow rate of up to 20,000 pounds per hour of storage potato capacity.
Increase Yields
Vanmark peeler machines only peel what you want to remove, which results in higher yields and less product loss.
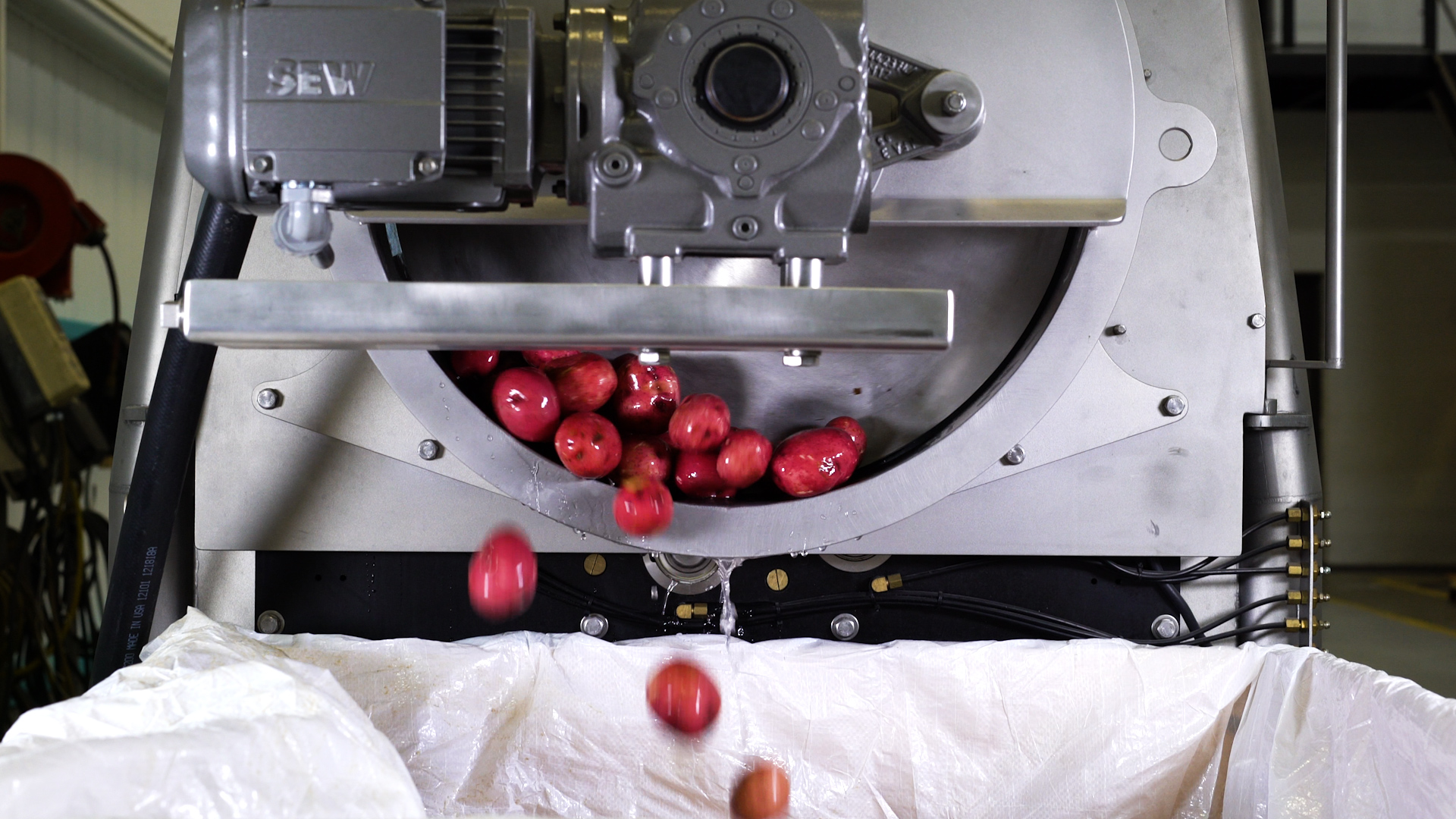
If you’re expanding your production capacity by automating manual peeling processes or upgrading from a low-end machine with poor quality or yields, a Vanmark potato peeler is the answer.
Increase Uptime
Our potato peeling machines are easy-to-maintain and operate, significantly decreasing downtime. In addition to designing our equipment to perform simple and quick cleaning and sanitation, Vanmark offers an optional Clean in Place (CIP) system that effectively cleans the rolls and peeler bed during sanitation and production.
Improve Water Savings
It’s important to consider water usage, treatment, and the ensuing costs when purchasing a commercial potato peeler. Vanmark offers several water-saving solutions to help conserve fresh water by separating starch and solids and reducing the amount of water sent for treatment.
You’ll get a high-quality and consistent cleaning every cycle while saving water through increased efficiency. The cleaning cycle lasts less than 10 minutes, and our CIP system works with all roll types, including sinewave, grit, and brush.
Versatility
Vanmark equipment enables you to diversify your product mix easily with flexible machines and roll/parts changeouts. Vanmark machines can peel/scrub/wash, and you can change out rolls and other parts according to the product you’re peeling, or as the potato makeup evolves throughout the season.
Vanmark peelers combine rugged durability, high performance, and ease of use. Potatoes are tumbled through a configurable combination of spray bars, four or six roller types, and other optional features, speeds, and settings to ensure the utmost flexibility and effective peeling, scrubbing and washing process.
Changing out the rolls on a Vanmark machine only takes a couple of hours for your line to prepare for changing variables or for the new season. Check out the video below to see just how easy it is to perform a roll changeout:
Decrease Labor Requirements
You won’t have to hire additional skilled labor to maintain or run Vanmark peelers. As such, you can focus on improving and being more confident in growth plans with less reliance on labor.
Most manufacturers can get by with their current maintenance team thanks to the simplicity of Vanmark machines and their ability to be worked on by maintenance crews. This is a massive benefit in a tight labor market.
Improve Profitability
Vanmark designs our peeler machines with profitability in mind. Thanks to our simple yet innovative peeler designs, you’ll experience greater product yields and less waste.
The savings don’t stop at our peelers—our Waste Separating Auger will allow you to filter solid waste out of process water which reduces waste to the drain system and resulting water treatment costs. You can then collect the solid waste from a self-cleaning screen for resale.
Manufacturer Support
Vanmark is a partner you can lean on for expert technical training, support, and maintenance. We offer pre and post-sale support, which is why more industry icons trust Vanmark peelers and view us as the go-to, trusted source for help. However, we also specialize in helping smaller companies grow and scale.
Large processors—Vanmark collaborates and responds quickly to the needs of larger companies, and we take their feedback into close consideration for future development. We work closely with their R&D departments to improve the performance of our machines.
Smaller regional processors—We apply the expertise gained from working with some of the largest potato chip processors in the world and apply that knowledge to help smaller processors grow.
We also provide the equipment used on a production line before and after the peeler machine; we can help you design the entire line. We’ll even make recommendations about parts that we don’t manufacture.
Our customers appreciate our dedicated service and support, and that our equipment is easy to use. Even those without technical know-how can operate our machines. We offer documentation, training videos, and in-person support to ensure we deliver top-notch customer service.
Vanmark potato peelers are easy to install and integrate with other equipment on your processing line. We have a detailed manual to help with the process. However, if installation issues arise, we can talk you through it over the phone to ensure it gets set up correctly.
Long-Term Success
Our potato peelers will set you up for long-term success with durable equipment that lasts for decades. While they’re not the lowest priced option on the market, you will continue to see an ROI on your Vanmark peeler as your production capacity increases and the machines are running full tilt for many years.
Vanmark peelers don’t require operators to keep them running, nor do they need a lot of adjustments. They’ll run for 20 to 30 days without interference from staff. When they need to come offline, part changeouts are quick and easy to get the machine back up and running. This helps significantly reduce reliance on a tight labor market.
Small Potato Chip Processer Scales Up - Case Study
Watch the video below that details how Vanmark helped a Downey’s - a small potato chip processor - scale up production through our 1820 Model Peeler/Scrubber/Washer.
Accelerate Your Growth With Vanmark Potato Peelers
Having the right potato peeler equipment on your production line will allow you to scale potato chip production quickly without sacrificing quality, speed, or efficiency. At Vanmark, we’re here for you every step of the way. Click below to learn more about our industrial potato and produce peeling equipment.
How to Calculate Industrial Potato Processing Equipment Payback and ROI