Distributors and switchers are two solutions that deliver product to multiple hydrocutters. However, only one offers more throughput, eliminates additional downtime, and features a longer lifespan.
Distributors and switchers are two solutions that deliver product to multiple hydrocutters. However, only one offers more throughput, eliminates additional downtime, and features a longer lifespan. Read on to learn more about using a distributor vs. switcher in hydrocutting potatoes and produce.
What are Switchers and Distributors in the Hydrocutting Process?
Distributors and switchers are two equipment solutions that send food products like potatoes, cucumbers, carrots, peppers, and more to a cutter head where they’re cut into French fries, pickles, matchsticks, and wedges. If a plug or a maintenance need occurs, these solutions move or shift flow to another hydrocutter to avoid costly downtime. While they sound similar, the distributor offers superior flexibility and production.
Switchers
With a switcher, product runs through a single cutting head or one side of a twin hydrocutter. If there's a plug or an operator needs to change out a hydro tube or cutter box, the product flow is switched to the other side or head automatically--eliminating downtime. Switchers use mechanical movement and moving parts to divert flow.
While having this flexibility is ideal for keeping high-volume production running, there’s an even better solution.
Distributors
A distributor divides the product into two outlets, enabling processors to send product through two cutting heads simultaneously and doubling throughput with one pump. If a plug or changeout is needed, the distributor automatically switches flow to the operational hydrocutter. With a distributor, processors get the benefits of a switcher, plus increased production.
Not only can the distributor be used to split product flow between two hydrocutters, it can also be used to direct product between a hydrocutter and a separate pipe run that carries it to a mechanical cutter or another part of the plant.
Its unique design has no mechanical assist (or moving parts.) The distributor can essentially be installed and run without worrying about repeatedly replacing moving pieces, like with a mechanical switcher. This translates to lower maintenance/upkeep costs. Not having moving parts also eliminates water leakage and leads to dependable performance and long life.
|
DISTRIBUTOR
|
SWITCHER
|
Use Case
|
Divide product flow to two streams – twin hydrocutters or hydrocutter and other application (i.e. mechanical cutter) at the same time
OR
Switch flow to either stream in the event of a plug or blade changeout
|
Switch product flow to one of two cutterheads in the event of a plug or blade changeout
|
Plug Handling
|
Switch flow automatically
|
Switch flow automatically
|
How Flow is Diverted
|
Pneumatically actuated ball valves. No mechanical assist or moving parts
|
Pneumatic cylinders with flexible tube and sliding seal plate
|
Throughput
|
Doubled via two streams flowing simultaneously
|
Single stream
|
Maintenance
|
None. No moving parts
|
Regular replacement of parts, including: flexible tube, o-ring seals, pneumatic cylinder, sliding seal plate, oiler lines for lubricating slide plate
|
Water Usage
|
None. Distributor remains fully sealed during operation
|
~1-2 gallons of leaking/splashing during switching motion unless frequently tuned
|
Product Damage
|
None. No disruption to flow due to ball valves and flow gates
|
Momentary damage to product in flow during mechanical switch
|
Supplier(s)
|
Vanmark (patented)
|
Various
|
Download this Distributor vs Switcher comparison table now
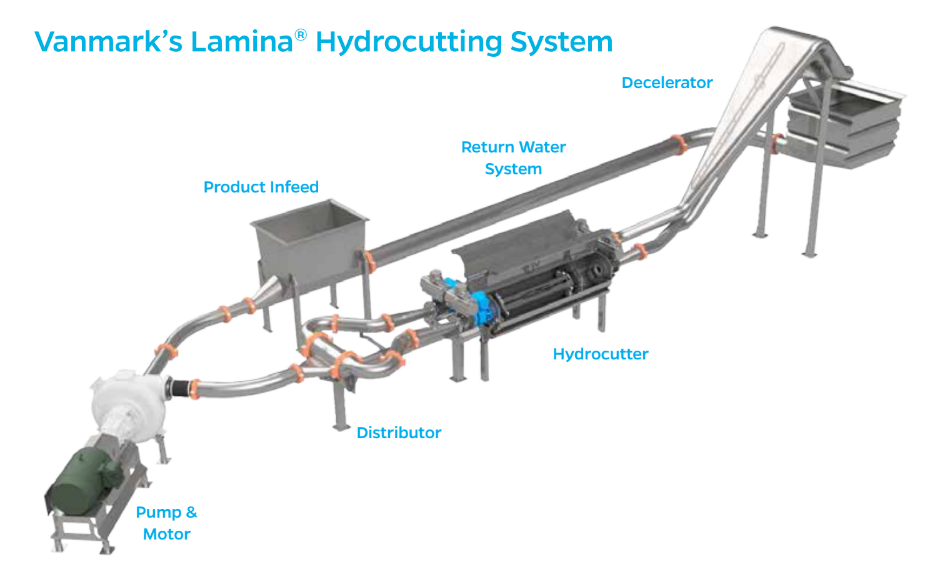
Upgrade Today for Increased Performance and Value
The Vanmark Distributor is part of a twin Lamina Hydrocutting System, the equipment of choice for the largest food processors in the world, cutting the French fries, pickles, carrot sticks, and more foods we know and love to eat. Our hydrocutting systems are designed for unmatched accuracy and consistent cuts, high volume throughput with no downtime, and simple maintenance. Click below to learn more about what you can expect from Vanmark hydrocutters.
Lamina Hydrocutting System