Whether you’re a small or large processor of potatoes to produce chips, fries or other frozen products, industrial potato processing equipment can help increase yields, decrease waste, and improve
Whether you’re a small or large processor of potatoes to produce chips, fries or other frozen products, industrial potato processing equipment can help increase yields, decrease waste, and improve overall efficiency. The challenge lies in finding the right machinery for your facility.
Flexibility, product handling, and continuous operation are just a few of the many things you’ll need to consider before making an informed purchasing decision.
Water Usage
The associated costs of water usage and treatment can be very high for industrial potato processing machines. This is why selecting processing machinery that helps reduce water consumption is essential.
The Vanmark Peeler/Scrubber/Washers and the Lamina Hydrocutting system have available features and options that help conserve freshwater by separating starch and solids while reducing water sent for treatment. For example, a waste separating auger and water reclamation system work with peelers to help reduce water usage by up to 90%.The return water line of the Lamina hydrocutter creates a “cyclone” effect that pushes denser starch water to the outer edge of the pipe and then skims it out for treatment. This means that more starch is being removed per gallon of water, with less water drained from the system and sent to treatment.
Product Handling
The equipment should handle potatoes gently with no breaking, bruising, scuffing, or skinning. This is easier said than done as potatoes can be fairly delicate and can easily sustain breakage on a processing machine that hasn’t been engineered to avoid damage. Bulk bins must also have a “first-in, first-out” conveyor system to prevent potatoes from sitting at the bottom and rotting.
Continuous Operation Capability
Long production cycles require equipment that offers continuous operation capabilities, which is essential for higher volume production processing facilities. Continuous operation potato processing equipment offers many advantages, such as decreasing storage space, reducing processing and holding time, and higher production rates.
Ease of Cleaning & Sanitation
Industrial potato processing equipment should also be easy to sanitize and clean. The easier sanitation is, the less time it takes, which reduces overall downtime. Especially for larger processors, downtime is costly and must be eliminated wherever possible.
Machinery with toolless processes is much easier and faster to clean and sanitize. This is critical as a thorough cleaning will help avoid food safety issues and contamination, which can lead to fines, recalls, and drops in sales and brand perception.
All equipment components should have a washdown rating to withstand your chemicals, cleaning frequency, and other sanitation procedures. The washdown capability of a machine is critically important as some machines are more complex than others, therefore their components can’t easily be sprayed down, which adds to downtime.
The equipment should also be able to withstand your production environment without corroding. For example, Vanmark often uses 316 stainless steel (less corrosive) in harsh environments like pickle production, where brine and other chemicals in the air may lead to corrosion.
During the initial engineering stages of a process, your engineers will go over the design of the equipment you buy to ensure there are no potential harborage points—places where bacteria and gunk can catch and build up over time.
Flexible or Custom Configuration
Every application is different and has many variables that can change throughout the year or from shift to shift. Because of this, having flexible equipment that can adapt to these changes is vital.
For example, continuous operation on Even Feeders helps keep product handling and peeling consistent (the flow is constant). Peeler discharge gates should be adjustable to increase/reduce peel levels.
Plant space and line layouts are always different, so the equipment layout needs to be configured to fit (space is a premium).
Durable
Durability is paramount as the machines need to last for decades and run for hours at a time. Look for potato processing equipment with a simple design, minimal moving parts, and a low maintenance cost.
Vanmark machines are built to last, provided that the customer takes good care of them. Most of our potato processing equipment is made out of 304 stainless steel, but we use other types of stainless steel at times (for example, 316 stainless) if the application requires it.
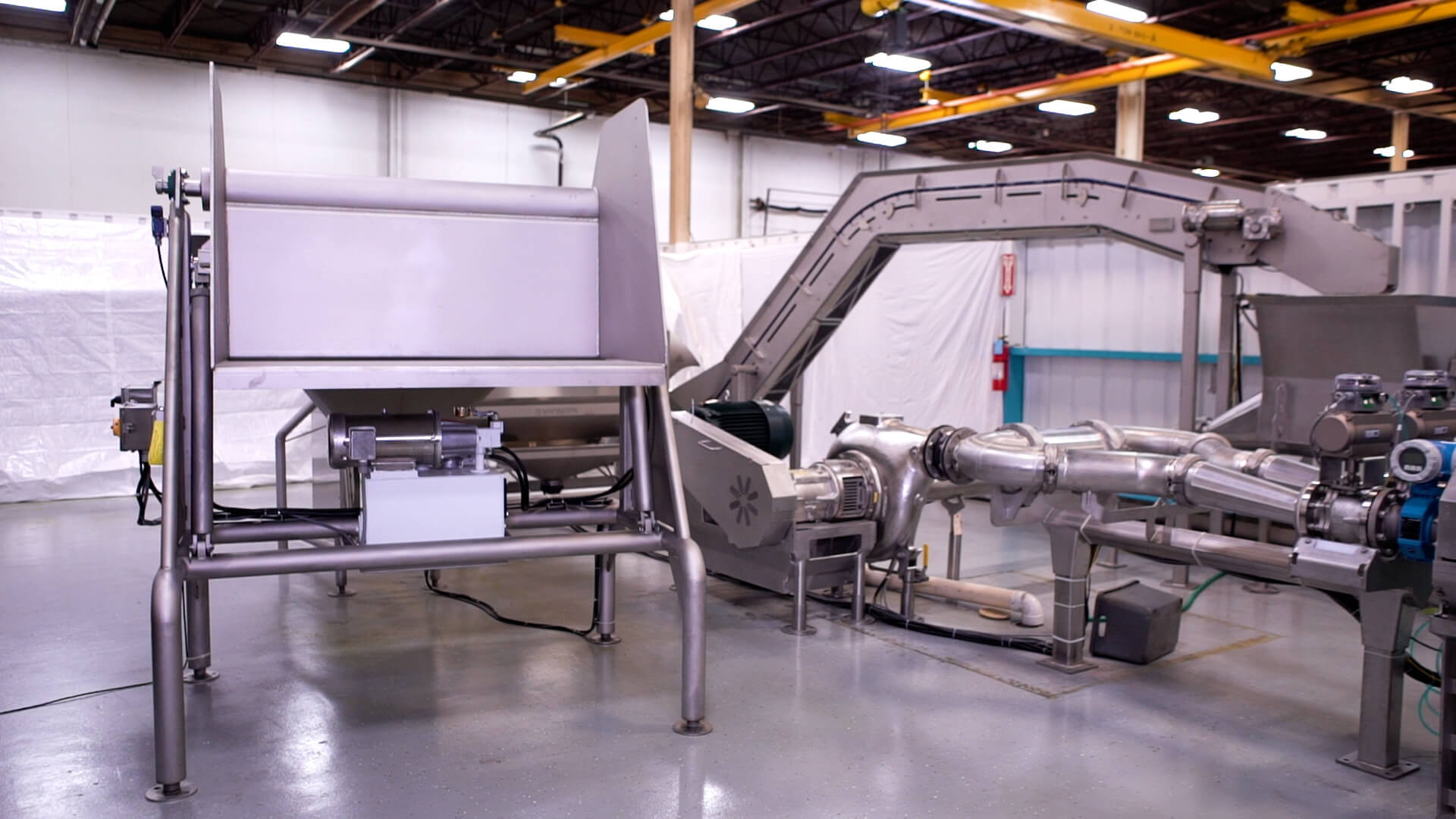
They're durable because they're well-designed and well-built. We don't cut any corners in the design or manufacturing in order to ensure that each machine that leaves our dock can hold up against any foreseeable conditions out in the field.
Low Maintenance
Some potato processing equipment, such as industrial potato peeling machines, require regular maintenance, such as switching out rolls for new ones. You’ll need to consider how hard or easy it is to perform change outs on a machine.
Required maintenance schedules, such as part replacements and inspections, are just as important. The more frequently they’re required, the more downtime and costs the machines incur. Big potato processors run full-tilt for days on end and can’t have machines offline for too long.