Discover the various signs that indicate it’s time to step up from manual to automated potato chip processing equipment. Click to find out what you should know.
When you want to level up your potato chip production, quality, and business, it’s time to start planning a move from manual to automated potato chip processing.
The good news is that while several key players dominate the potato chip market, there’s plenty of elbow room (and consumer cash) to go around. Forecasts have indicated that the market is only growing and will reach $50.1 billion by 2028.
However, automating your processing can come at a relatively steep upfront cost. The initial outlay of capital might seem unworldly.
Read on to learn more about the signs it’s time to automate and how long-term improvements and opportunities can give you a positive ROI and peace of mind regarding the investment.
Manual/Slow Processes
Manual potato chip manufacturing processes require each step to be performed by hand, leading to a slow and limited production pace. If you land a new contract or business suddenly increases, you’ll need to scramble if you’re already running at capacity.
This approach could work for a while, but it’s not sustainable. Cracks in your processes will eventually form and you’ll end up with an even bigger problem down the line.
In contrast, automating creates a much more efficient manufacturing process, resulting in higher productivity and reduced manufacturing costs.
Product Waste
Peeling potatoes by hand leads to peel loss and lower yields. Automatic potato peelers, such as those from Vanmark, are designed with increased yields in mind. Best of all, machines don’t get tired or start slowing down in the final few minutes leading up to a shift change.
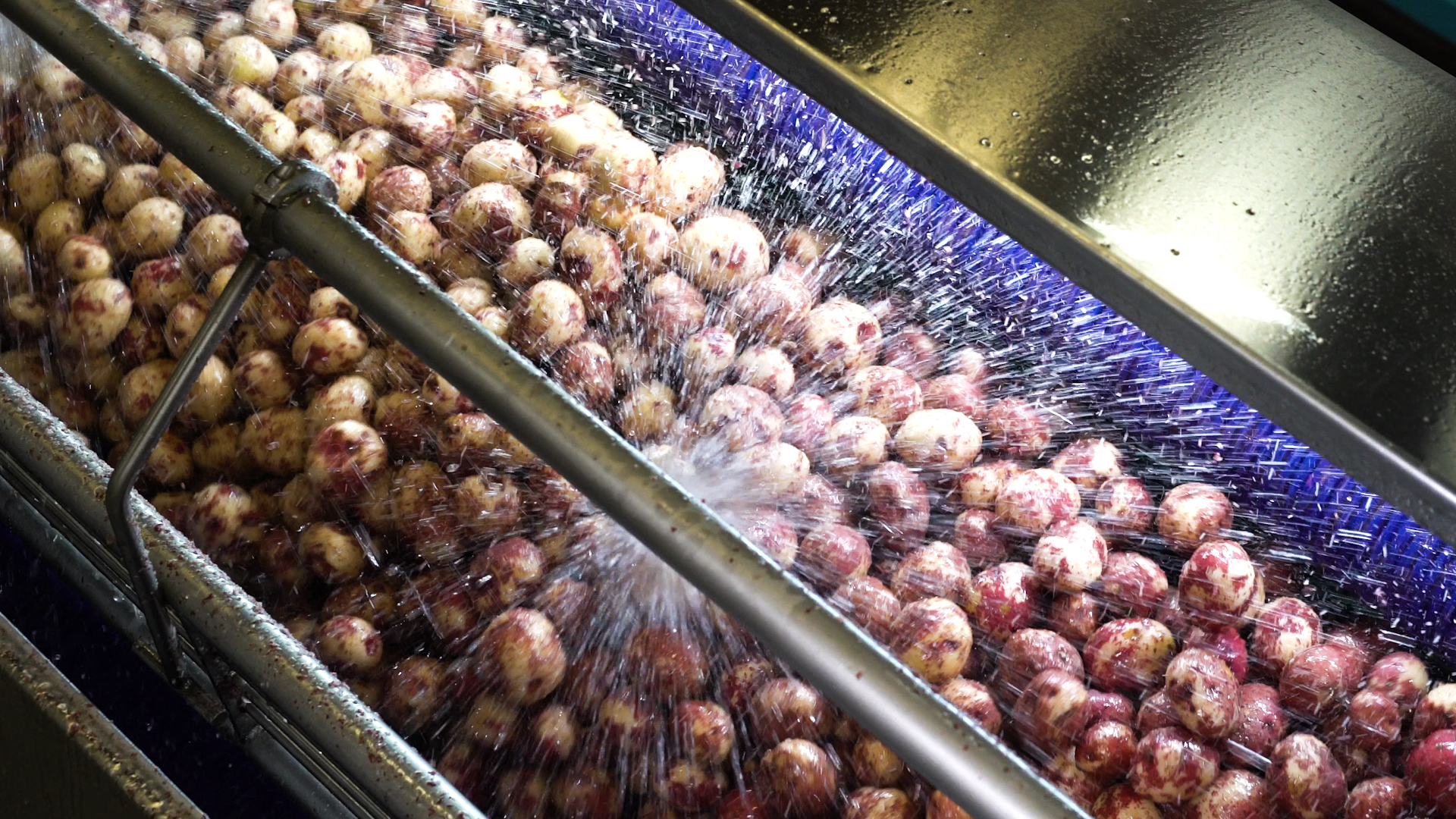
Labor Challenges
Labor shortages are a growing concern for many food processing companies. Worker retirement, market changes, and the continued fallout from the pandemic of 2020 are all contributing factors.
Work-related accidents tend to increase when companies rely upon inexperienced or untrained workers to fill the gap. This also can result in lowered levels of efficiency and productivity as
new workers can take several months to get up to speed.
Automated potato chip processing equipment will never call in sick or get injured on the job.
Inconsistent Quality
When tasks such as peeling, slicing, frying, and packaging are performed manually, it can lead to waste and variations in the quality of the end product. Human error and fatigue can result in potato chips that are not of a consistent quality, thickness, or have been damaged during the production process.
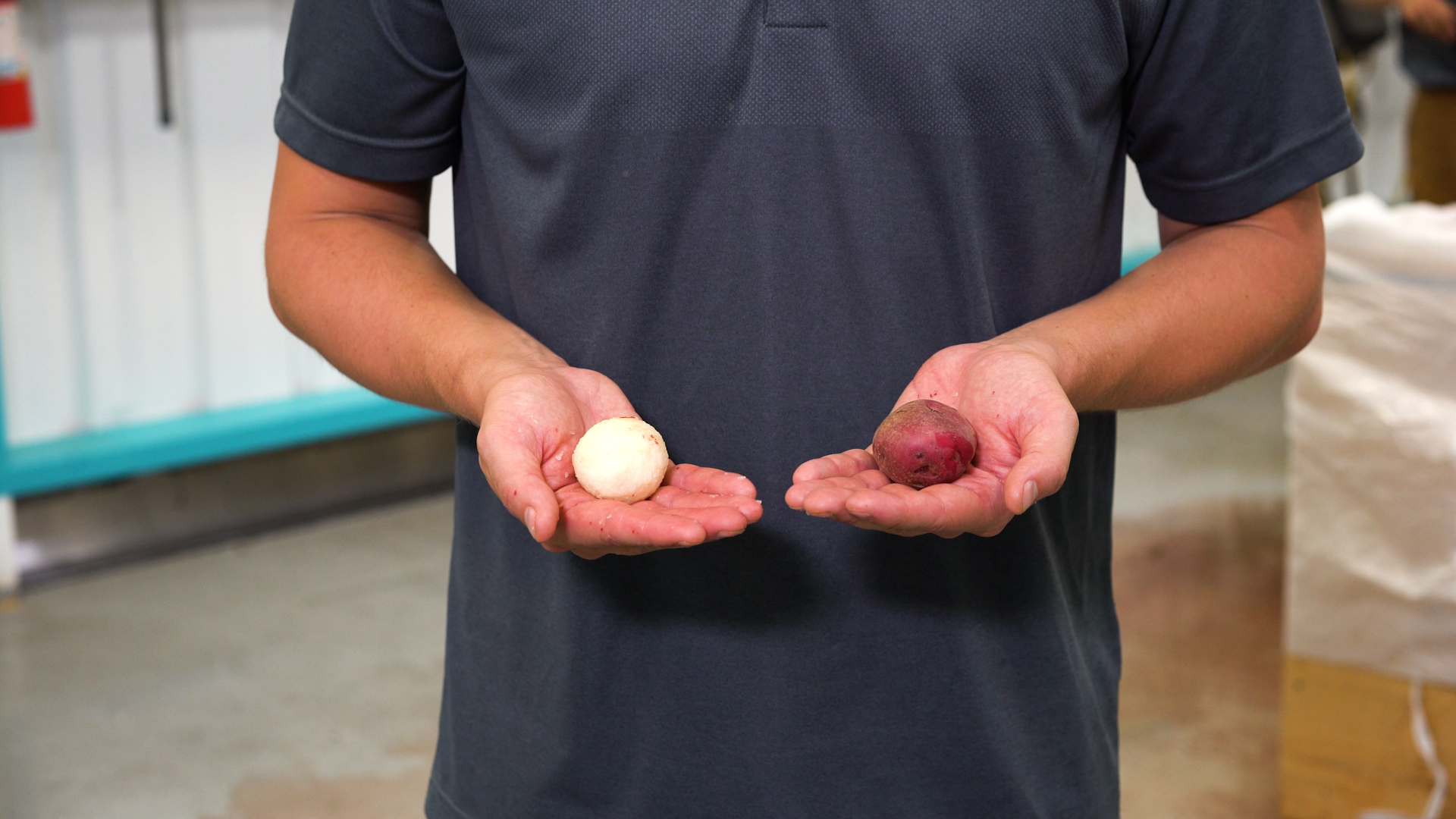
For example, an issue that many smaller potato chip processing companies face is oil-takeup, or how much fryer oil the chips absorb. This is directly affected by how well the potatoes are manually sliced and pre-treated.
Inconsistent quality can have a significant negative impact on the reputation of an emerging potato chip manufacturer. Customers may be less likely to purchase chips that vary in quality from bag to bag. Obviously, this can reduce sales, harm your reputation, and make it more challenging to compete in the market.
Regular Stoppages and Downtime
Manufacturing potato chips by hand can lead to regular work stoppages and downtime. Machines might break down because they’re not designed to handle existing workloads, and workers may require breaks or time off.
The need for comprehensive sanitation and maintenance also leads to regular downtime and production stoppages. In contrast, Vanmark designs our potato chip processing machines for quick, easy, and thorough sanitation and cleaning.
Safety Concerns
Manufacturing potato chips by hand can expose workers to hazards such as cuts from sharp equipment, hot oil burns, or slips and falls from wet floors. Just because your facility hasn’t experienced a major accident doesn’t mean it can’t happen.
All it takes is for one employee to have an “off day” or not pay attention, and you’re suddenly dealing with a costly workers’ compensation claim—and that could draw the potential ire of OSHA and other regulatory agencies.
Automated potato chip processing can significantly reduce the risk of workplace injuries and accidents, which are inherent in manual processing operations.
Automate and Grow With Vanmark Potato Chip Processing Equipment
At Vanmark, we have decades of experience helping potato chip manufacturers scale up through our automated equipment. We design our potato chip processing machines for high performance and rugged durability. You’ll be able to increase volume and realize an ROI faster than competing equipment. Click below to learn more.
See Our Potato Chip Processing Equipment